In the manufacturing world, reducing machine downtime is crucial for optimizing production and improving overall efficiency. Tracking machine downtime provides valuable insights into operational performance, but the real power of downtime tracking comes when you analyze the data effectively. By analyzing downtime data, manufacturers can pinpoint recurring issues, improve processes, and implement targeted solutions that minimize downtime and maximize productivity. This article discusses the importance of downtime data analysis and how manufacturers can use it for continuous improvement.
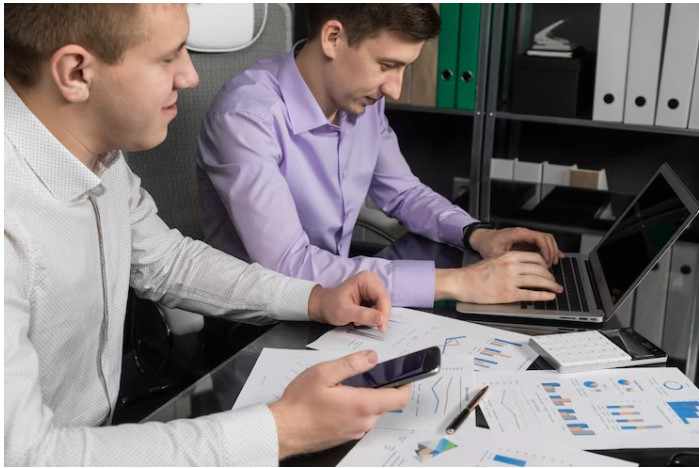
Why Analyzing Downtime Data Matters
Machine downtime tracking is only valuable when the data collected is analyzed and used to inform decision-making. Without analysis, downtime tracking becomes just a record of events without actionable insights. Properly analyzing downtime data can uncover inefficiencies, prevent unplanned downtime, and lead to long-term improvements in equipment reliability and production output.
By consistently analyzing downtime data, manufacturers can create a cycle of continuous improvement where processes are constantly refined, and downtime events are reduced over time. The insights gathered from downtime tracking can inform decisions related to maintenance, production scheduling, and resource allocation, ultimately driving higher productivity.
Key Steps in Analyzing Downtime Data
1Collect Accurate and Consistent Data: The first step in analyzing downtime data is ensuring that data collection is accurate and consistent. This requires employees to be properly trained on how to log downtime events correctly and consistently. Make sure that downtime tracking systems are integrated with real-time monitoring tools and that data is entered immediately, with key details such as downtime duration, cause, and affected equipment. Accurate data collection is essential for meaningful analysis.
2.Categorize Downtime Events: Once data is collected, categorize downtime events based on their causes. Common categories include:
Mechanical Failures: Breakdowns or malfunctions of equipment components.
Operator Errors: Mistakes made during machine operation.
Maintenance: Scheduled or unscheduled maintenance activities.
External Factors: Issues such as power outages or supply chain disruptions.
1.Categorizing downtime events helps identify recurring patterns, allowing manufacturers to pinpoint root causes and prioritize areas for improvement.
2.Calculate Key Metrics: Key performance metrics should be calculated to assess the effectiveness of downtime management. Some of the most important metrics include:
Mean Time Between Failures (MTBF): The average time between equipment failures. A higher MTBF indicates better equipment reliability.
Mean Time to Repair (MTTR): The average time it takes to repair equipment after a failure. A shorter MTTR signifies more efficient repair processes.
Total Downtime: The overall amount of time equipment is non-operational during a specified period. Monitoring this metric helps track improvements in downtime reduction.
1.These metrics can be tracked over time to measure the effectiveness of maintenance practices, identify high-risk equipment, and assess the impact of downtime reduction initiatives.
2. Identify Trends and Patterns: One of the primary goals of downtime data analysis is to uncover trends and patterns that may point to systemic issues. For example, if downtime data consistently shows that a specific piece of equipment is frequently down due to mechanical failures, it may indicate that the equipment is nearing the end of its lifecycle or that it requires more frequent maintenance. Analyzing downtime patterns enables manufacturers to identify the root causes of downtime and address them before they result in more significant problems.
3.Use Root Cause Analysis (RCA): Root Cause Analysis (RCA) is a systematic process used to identify the underlying causes of downtime events. Instead of simply addressing the symptoms, RCA digs deeper to find the fundamental issues that contribute to equipment failures or downtime. For example, if operator errors are causing machine downtime, the root cause might be insufficient training or unclear operating procedures. Conducting regular RCA sessions helps identify areas that need improvement and prevent recurring downtime events.
4.Implement Corrective and Preventive Actions: Once the causes of downtime have been identified, it’s important to take corrective and preventive actions to mitigate future occurrences. Corrective actions focus on resolving the immediate issue, while preventive actions aim to avoid similar downtime events in the future. For example, if equipment breakdowns are a common issue, preventive actions might include upgrading machinery, improving maintenance procedures, or introducing predictive maintenance tools.
1.Both types of actions should be documented and tracked to ensure continuous progress in reducing downtime.
2.Review and Adjust Maintenance Strategies: Downtime data analysis can provide valuable insights into the effectiveness of your maintenance strategies. If data shows that downtime is often caused by failed components, you may need to adjust your maintenance schedule to address parts before they fail. Using data-driven insights to optimize preventive and predictive maintenance strategies can help reduce unplanned downtime and improve equipment reliability.
3.Monitor and Evaluate Continuous Improvement: Continuous improvement is key to reducing downtime over time. Set clear performance goals and regularly review downtime data to assess whether corrective and preventive actions are working. Use the feedback gathered from ongoing analysis to refine your processes and keep driving improvement.
Benefits of Analyzing Downtime Data for Continuous Improvement
1.Reduced Unplanned Downtime: By identifying trends and addressing root causes, downtime data analysis helps reduce unplanned downtime, ensuring that production schedules are maintained without disruption.
2.Improved Equipment Reliability: Analyzing downtime data allows manufacturers to implement predictive maintenance strategies, improving the reliability and lifespan of equipment.
3.Increased Productivity: With less downtime and more efficient operations, manufacturers can increase overall productivity and throughput, leading to better performance and greater profitability.
4.Cost Savings: Reducing downtime means fewer emergency repairs, less overtime, and optimized resource allocation, which leads to significant cost savings.
Conclusion
Analyzing downtime data is an essential practice for driving continuous improvement in manufacturing. By identifying trends, conducting root cause analysis, and implementing corrective actions, manufacturers can minimize downtime, improve equipment reliability, and optimize overall operational efficiency.
For more information on machine downtime tracking and how to analyze downtime data for continuous improvement, please contact us at 1.888.499.7772. Our team of experts is ready to help you implement effective downtime tracking and data analysis strategies that enhance your operational performance.
SourceUrl:-https://thedigitalexposure.com/how-to-analyze-downtime-data-for-continuous-improvement/
Write a comment ...