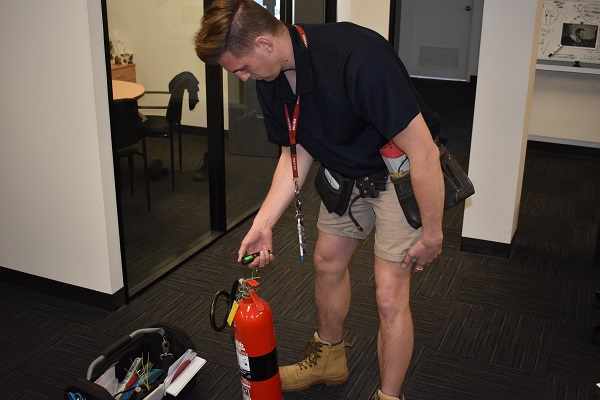
Finding fire extinguisher test services? Adelaidetestandtagging.com.au is a renowned fire extinguisher testing company. We provide top class testing and tagging services at a competitive price. Do visit our site for more info.
Finding fire extinguisher test services? Adelaidetestandtagging.com.au is a renowned fire extinguisher testing company. We provide top class testing and tagging services at a competitive price. Do visit our site for more info.
Write a comment ...
In the manufacturing world, reducing machine downtime is crucial for optimizing production and improving overall efficiency. Tracking machine downtime provides valuable insights into operational performance, but the real power of downtime tracking comes when you analyze the data effectively. By analyzing downtime data, manufacturers can pinpoint recurring issues, improve processes, and implement targeted solutions that minimize downtime and maximize productivity. This article discusses the importance of downtime data analysis and how manufacturers can use it for continuous improvement.
In today’s competitive manufacturing environment, machine downtime can significantly impact productivity and profitability. One of the most effective ways to mitigate the effects of downtime is through accurate and proactive downtime tracking . However, implementing downtime tracking systems is only part of the solution. Ensuring your team is properly trained in using these systems is crucial for achieving maximum efficiency and reducing downtime. This article explores best practices for training your team on effective downtime tracking practices and highlights the benefits of having a well-informed workforce.
In today’s fast-paced manufacturing environment, maximizing equipment uptime is critical to maintaining productivity and minimizing costs. To achieve this, manufacturers need an efficient and streamlined way to monitor, track, and manage machine downtime. One of the most effective solutions is integrating machine downtime tracking with an existing Enterprise Resource Planning (ERP) system. This integration allows for seamless data flow between production, maintenance, and other departments, enabling companies to identify and address downtime more effectively.
In manufacturing, machine downtime can disrupt production schedules, increase operational costs, and negatively affect supply chain performance. When equipment is down, the entire manufacturing process can be delayed, leading to supply chain bottlenecks, missed delivery deadlines, and reduced customer satisfaction. Effective machine downtime tracking is essential to identify and mitigate the risks posed by unplanned downtime and ensure smooth, efficient supply chain operations.
In manufacturing, machine downtime is an inevitable part of operations, but minimizing its impact is crucial for maintaining productivity and profitability. One of the most effective ways to manage downtime is through the implementation of downtime tracking systems. This article explores several case studies of companies that have successfully adopted downtime tracking systems, demonstrating the significant benefits these solutions can bring to manufacturing operations.
In the manufacturing industry, managing and minimizing machine downtime is crucial to ensuring consistent productivity and profitability. One of the most effective ways to reduce downtime is through the implementation of equipment downtime tracking software. However, choosing the right software can be a daunting task given the many available options. This article outlines the key factors to consider when selecting the best downtime tracking software for your business.
In the competitive landscape of manufacturing, minimizing machine downtime is vital for enhancing productivity and profitability. Effective tracking of machine downtime allows manufacturers to gain insights into operational efficiency and identify areas for improvement. This article explores the essential strategies for tracking machine downtime and optimizing equipment performance.
As industries evolve, the way manufacturers manage machine downtime is undergoing a significant transformation. Machine downtime tracking is no longer just about recording periods when equipment is not operational; it is now integrated with advanced technologies that enhance operational efficiency and decision-making. This article explores the future of downtime tracking, highlighting emerging technologies and trends that are shaping this critical aspect of manufacturing.
In the manufacturing sector, equipment reliability is paramount for ensuring operational efficiency and minimizing costs. Machine downtime not only affects productivity but can also lead to significant financial losses. Therefore, implementing effective downtime tracking mechanisms is essential for maintaining high levels of equipment reliability. This article explores the importance of machine downtime tracking and its role in enhancing equipment reliability.
In the manufacturing industry, efficient downtime tracking is crucial for maintaining productivity and optimizing equipment performance. The integration of data analytics into downtime tracking processes has emerged as a game-changer, offering deeper insights and more effective management strategies. This article explores how leveraging data analytics can enhance downtime tracking and improve overall manufacturing operations.
In the competitive world of manufacturing, minimizing machine downtime is essential for maximizing productivity and maintaining operational efficiency. Effective downtime tracking plays a pivotal role in achieving these goals by providing insights into equipment performance and identifying areas for improvement. This article explores the benefits of effective downtime tracking and how it can enhance your manufacturing operations.
Effective downtime management is crucial for maintaining productivity and minimizing operational disruptions in manufacturing environments. Implementing a robust downtime management program involves a combination of strategies, tools, and best practices to track, analyze, and mitigate downtime events. This article outlines key best practices for establishing a successful downtime management program and optimizing equipment performance.
The advent of Industry 4.0 technologies has transformed manufacturing practices, bringing significant advancements in automation, data analytics, and real-time monitoring. One of the key areas where these technologies are making a profound impact is in the prevention of machine downtime. By integrating advanced solutions for machine downtime tracking and equipment management, Industry 4.0 technologies are revolutionizing how manufacturers address and minimize downtime.
Preventive maintenance is a cornerstone of effective downtime management in manufacturing environments. By proactively addressing equipment issues before they escalate into costly breakdowns, companies can minimize downtime, improve operational efficiency, and enhance overall productivity. This article explores the importance of preventive maintenance and its impact on reducing machine downtime in manufacturing facilities.
In the fast-paced world of manufacturing, every minute counts. Any interruption in production can lead to significant losses in revenue, productivity, and customer satisfaction. That's why effective downtime management is crucial for manufacturers looking to stay competitive in today's market.
In today's fast-paced manufacturing environment, minimizing downtime is essential for maintaining productivity and competitiveness. Every minute of downtime equates to lost revenue and potential disruptions in the supply chain. To address this challenge, manufacturing companies are increasingly turning to advanced strategies for downtime management. In this article, we'll explore some of the top strategies that production facilities can implement to minimize downtime effectively.
In the realm of manufacturing, downtime can be a significant hindrance to productivity and profitability. Whether caused by equipment failures, maintenance activities, or operational inefficiencies, every minute of downtime translates into lost production time and potential revenue. To address these challenges effectively, manufacturing firms are increasingly turning to real-time monitoring solutions for enhanced visibility into production downtime. This article explores the benefits of real-time monitoring and its role in optimizing production processes.
Want to know the requirements for RCD testing? Adelaidetestandtagging.com.au can help. RC testing requirements maintain safety. We offer a comprehensive range of services, including electrical testing, pressure testing, and tagging. Check out our site for more details.
At Adelaidetestandtagging.com.au, we provide comprehensive testing and tagging services for Adelaide and its surrounding areas. Our experienced team of professionals ensure your safety with the highest quality service. Don't take chances with your safety - trust the experts at Adelaide Test and Tagging!
Write a comment ...